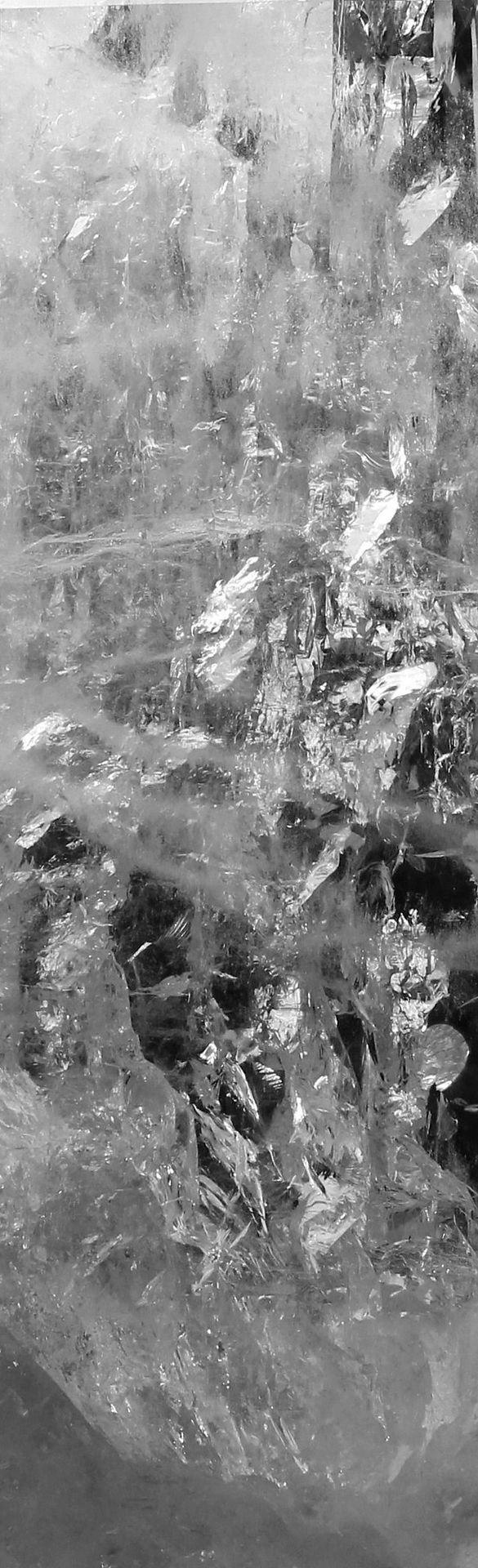
Project IMPURITY
An Interactive Projection Mapped Quartz Model
by Amanda Grace
SIDE EFFECT
In this phase of Project IMPURITY, my focus is on planning and developing the project further into a functional demo. 3D printing is the next step for a closer prototype that has a controlled amount of Quartz faces so that the projector can project the Quartz texture and color clearly and realistically. Next the hope is to make all 4 impurity effects on Quartz work in real time
as an individual adjusts the impurity bars in the TouchOSC app. Preferably, the demo would be activated by this app on a tablet. Currently, the app is being tested on an Iphone.
STORYBOARD SCRIPT
-
Person approaches 3D model
-
Project Impurity appears above 3D model
-
Projector projects constantly onto model with “get started prompt” (crystal is white)
-
Person approaches project (show crystal 3d object and tablet in same shot)
-
Person picks up tablet and sees crystal icon for app
-
Person opens app and sees Touch OSC impurity bars
-
Person sees text instructions prompt on wall
-
Text changes to Quartz information
-
Person moves impurity IRON making the crystal turn purple
-
Amethyst info appears as text
-
Person moves impurity TEMPERATURE making the crystal turn from purple to yellow orange
-
Citrine info appears as text
-
Person moves an impurity RADIATION making the crystal turn darker
-
Person moves impurity UV making the crystal lighter
-
Person may choose to reset crystal to quartz at any time to try combinations
-
Person learns what impurities cause what colors and color effects as well as what quartz is identified by based on color changes.
PROBLEM SOLVING
One projector will be used to project the Quartz texture onto the 3D printed model.
Due to this fact, ways in which to control how many faces face the projector were explored.
On the left, the image portrays an example of a 3D printed crystal group. If the IMPURITY Quartz model were to be projected on as a standing model, only one projector would not be able to project onto the back faces, resulting in an obvious shadow cast behind the model.
The middle image is an example I used as inspiration for a solution to the many faces problem.
In the example on the right, it is shown that a shape with faces can be attached to a wall. This would eliminate unnecessary faces for a simpler projection.



3D MODELING
Using Autodesk Maya, a classic Quartz tower was modeled, sliced in half, then the triangular faces were mirrored to the bottom. This creates a doubled terminated Quarts formation.
The model shown below is measured (in inches) to print large enough for the projector to project clearly onto all the faces as it is attached to a wall. The back of the model is completely flat for this to work with adhesive command strips.


3D Modeled Double Terminated Quartz Formation in Autodesk Maya
Wire frame view (left) Model view (right).
3D PRINTING
The process of 3D printing a Quartz crystal is tricky. Depending on the type of printing filament, the model may print well or need a few test prints or some remodeling of the
model to produce a clean print. With the help of Lee Cherry from the Design IT Lab,
tests were printed and solutions were made, but with a good amount of improvisation.

3D printing filament Polymaker PETG transparent
3D Printing Process and Problems
3D Printing Successes
PROJECTION TESTING
Unfortunately, the transparent filament purchased for this project did not turn out to be the best material to use for the planned projection. If the projection had been a solid color, then opaque material would work. For the sake of the project however, the white model must be the one to use that produces the best and most accurate visual results.
TIMELINE (based on studio days)
NOV 13 - Get impurity Iron to work in real time (adds purple)
NOV 14 - 3D print crystal model in PETG transparent filament
NOV 15 - Get impurity Radiation to work in real time (adjusts hue intensity)
NOV 20 - Get impurity Temperature to work in real time (color turns to citrine)
NOV 27 - Get impurity UV to work in real time (adjusts white tinting)
NOV 29 - Kantan map shapes to new 3d printed crystal/ Test
DEC 4 - Create Logo/UI icon for entering app - Put in info text to appear next to crystal
DEC 6 - Test all in Kantan Mapper/ TouchOSC
DEC 11 - Grad Review 1 - 5pm/ 5 min about the project
CONCLUSION
Even though the idea behind using transparent filament did not work for what the project is trying to achieve, the use of 3D printing for the model was still successful. A lot of improvisation was made and a lot was learned. The opaque material was great for mimicking the look of Quartz and the way it reflects light, but not for being projected onto. The audience needs to see a clearer color and texture on the model in order to interact with the impurity levels and color changes. Now that the model is done, the next steps are focusing on the impurities and making them change the color seen in real time using Touch Designer and TouchOSC.